9 Best Practices for Less Forklift Downtime
29/10/2020
Forklifts have changed dramatically over the years, but the basics of good fleet management haven’t changed nearly as much as the forklifts themselves. The tenets remain centered on operational and maintenance practices that can help save you from hassles, downtime and burgeoning repair costs.
WHAT IS THE AVERAGE LIFE EXPECTANCY OF A FORKLIFT? WHAT IS CONSIDERED HIGH HOURS ON A FORKLIFT?
On average, a forklift will last about 10,000 hours. Running eight hour shifts that averages out to around 2,000 hours per year or about five years. Properly maintained forklifts can last substantially longer, however, even eclipsing the 20,000 hour mark.
To learn just what these best practices are for minimizing downtime, we spoke with several forklift truck dealers with decades of experience with forklifts and fleet management. This is what the dealers told us:
1. KEEP RECORDS
The best way to know how your forklifts are doing is to keep records of each one. Each forklift is different, so an accurate performance profile will pinpoint the precise time when that forklift has outlived its usefulness.
It’s usually best to keep a separate record for each forklift. In your record, keep the truck’s vital statistics: purchase or lease price, date obtained, brand, model number and serial number. Add to this information the dates of all Planned Maintenance (PM) checkups and what, if anything, needed fixing by the service technician. Usually you’ll get a report sheet after every PM. Keep these sheets in the truck’s file for easy reference and to track repair trends and/or operator damage/abuse.
You also want to keep track of engine hours so you know how much that forklift is actually being used. This requires that an hour meter is working on each forklift.
2. KNOW THE FACTS
There are more than 1 million forklifts on the job across America today. Probably half are siphoning excessive dollars from their owners by working past their useful life.
To make sure your fleet isn’t a budget drainer, you need to know what each forklift’s ownership and maintenance costs are. To determine this, you need the information from your records and a few calculations.
The ownership cost for each forklift is the difference between its delivered cost and its residual value when traded in. For example, a forklift costs $15,000, is four years old and has accumulated 8,500 hours. Its trade in value is now $6,000. Subtract this from $15,000 to get $9,000, the ownership cost; then divide by the engine hours. You find that this forklift costs $1.06 per operating hour.
The cumulative maintenance cost is the total of maintenance labor and material cost from the date of purchase. Suppose in our example, maintenance totals $8,800. Again divide this amount by the engine hours to arrive at $1.04, the maintenance cost per hour.
This forklift is costing you $2.10 per hour to operate and maintain.
3. REPLACE FORKLIFTS AT THE RIGHT TIME
HOW LONG SHOULD A FORKLIFT LAST?
There is no simple answer for how long a forklift should last, but many people take a less than optimal approach to replacing their lift trucks. Some companies, without information from records, just replace their forklifts at a certain age, usually from three to seven years, depending on their application. The problem with this set policy is that only an accurate performance profile based on records will pinpoint the precise moment when a forklift has outlived its usefulness. Using a set time period will have you replacing some units before their lowest total cost and others after it has passed.
Look at the chart and notice the most cost-effective time to replace a forklift is at its lowest total cost point, also called its economic break-even point. After that, the maintenance costs rise and you may end up spending more than necessary to keep that forklift operating. And this doesn’t include the productivity lost and cost of downtime while the forklift is being repaired.
4. MATCH THE FORKLIFT WITH APPLICATION
Often when forklift dealers audit their customers’ operations, they find that forklift specifications do not match the jobs they’re currently expected to do. This can happen because your business and material handling can change over time. It may be that you’ve outgrown your warehouse area and have begun to store material on the floor or on racks that are closer together than in the past.
For optimum productivity, forklifts need to match the maneuverability and lift requirements of today’s application. If they don’t, you could be spending more to keep an overtaxed forklift running, or spending extra for a forklift that’s too powerful for the loads it’s moving. You could also have a fleet that’s underutilized, which could mean you need fewer units in your fleet.
If you haven’t had a forklift dealer perform a thorough audit in the past three years, call and request one soon. Your local forklift truck dealer can audit your operations well and do so at no cost to you.
5. PERFORM PLANNED MAINTENANCE
You wouldn’t operate your new car for three years without changing the oil or filters. You know that to keep an auto running well, you need to follow the manufacturer’s recommended maintenance schedule.
The same is true with forklifts. If you follow a maintenance routine, you’ll reduce downtime and overall operating costs by catching little irregularities before they turn into major repairs and significant downtime. Learn more about our planned maintenance and service programs.
6. READ THE MANUAL
Inside the operation and maintenance manual that comes with each forklift, you’ll find a maintenance section with scheduled service intervals. The manual also provides service details on proper replacement fluids and service specifications. Using the manufacturer’s specified fluids and replacement parts will ensure that your forklift gets what it was originally designed to use.
There is also information on proper operation and important safety considerations that are good to review with your operator. If you are missing the original manual that came with your lift truck, you can ask your local dealer to provide a new one.
7. TRAIN OPERATORS AND PAY ATTENTION
Training on proper forklift operation and forklift safety certification is required by the U.S. Occupational Safety and Health Administration (OSHA) in the United States, and is the law in most Canadian provinces.
In addition, it’s a great way to save costs. Damage to a forklift or products caused by poor operating practices can take a big chunk off your company’s bottom line. Take the time to observe operators at work. If you see them doing things that are against company policy or indicate they’ve forgotten the basics of proper forklift operation, you’ll know it’s time for refresher training. You might also find that special equipment like G-force meters, directional shift inhibitors, speed limit controls and other devices could maximize forklift and tire life, not to mention reduce product damage.
Training operators to perform a daily or pre-shift inspection routine can not only catch a potential safety issue but it can also help save you money. By addressing any issues the operators find during this inspection, you can help to reduce accelerated wear on moving parts, lower repair costs and possibly prevent a workplace incident.
8. PRACTICE GOOD HOUSEKEEPING
All the training in the world won’t prevent product and forklift damage if your facility is not kept clean and the floors or operating surfaces kept in good repair. Dust, dirt and debris can damage forklift components and systems. Uneven surfaces and wet or oily floors can impact forklift life and endanger the operators, or personnel in the area, by creating the potential for a workplace incident.
If you take pride in your facility and its cleanliness, you’ll find the forklift operators may catch “the spirit” and will take pride in their work.
9. DON’T GO IT ALONE
You don’t have to try to cover all the bases by yourself. Every one of our forklift dealerships can help with record keeping, operator training, maintenance programs and replacement information. They can also audit your facility and let you know which of these nine best practices need improving. Contact your local dealer to get started.
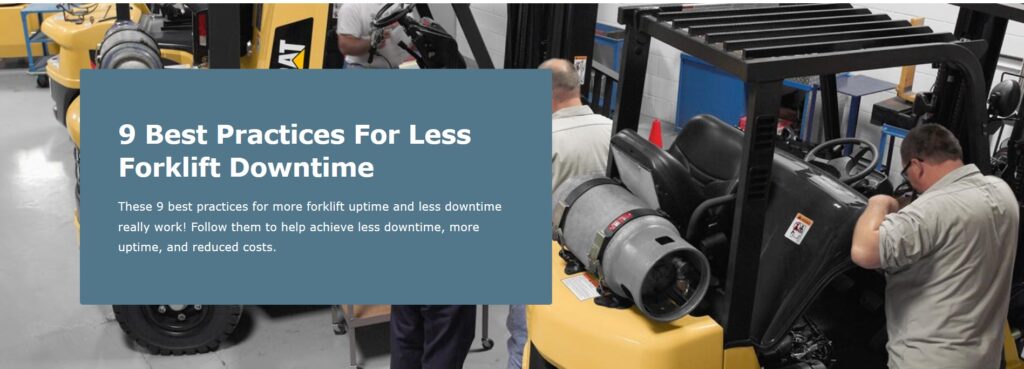