Better safe than sorry
01/10/2020
Getting the most out of your warehouse is a daily challenge for your logistics manager. A constant flow of goods needs to be maintained and customers must receive the items they order in time. The job becomes even more complicated when you store and ship dangerous or hazardous goods. Gian Schiava interviews a logistics real estate specialist to find out how facilities for these differ from ‘ordinary’ warehouses.
We meet up with Rene Geujen, Director Plan Development at Next Level Development, a specialist firm which develops and finances futureproof and sustainable logistics centres, to talk about this ‘dangerous’ topic.

Rene Geujen, Director Plan Development, Next Level Development.
Eureka: What adjustments need to be made in warehouses when it comes to the storage of dangerous goods?
Rene: In practice, the quantities you are storing really determine the adjustments to be made. Basically, we see three different levels with different outcomes. The first is simple adjustment. Hazardous items can be stored, up to a certain tonnage, in dangerous goods containers. Within this category, there are hardly any modifications to the building itself. This often applies when quantities of goods are smaller. The risk becomes more manageable when you spread these dangerous supplies all over the warehouse. Construction work is limited to ventilation systems and additional connections to fire control systems.
Second is inbuilt variation, also called the ‘box-in-a-box’ solution. Changes have to made to the building structure and foundation in order to obtain a certain fire resistance, like with double steel constructions. Spreading is again key. It is all about making choices about compartmentalisation: how large do spaces have to be and how flexible should you make these compartments? The hazard classification of the goods themselves also determines a lot. Will you store goods on pallet racking or as loose items on the warehouse floor? Which products do we have today and what do we expect tomorrow?
The last category is the real dangerous goods warehouse. ADR is the European Agreement concerning the International Carriage of Dangerous Goods by Road (ADR), which was created in Geneva in 1957 and entered into
force in 1968. Various national standards today are based on the ADR.
The ADR warehouse is a category of real estate on its own. It is purpose-built for storing and handling dangerous goods. Some of its features are:
– The total layout is different and it contains much fewer units
– It has a concrete roof and sometimes the whole construction is in concrete
– All the industrial doors are different – to contain extinguishing foam/water during fires, for example
– In an increasing number of cases, carbon dioxide fire extinguishing systems are implemented instead of foam or water sprinklers to extinguish fires as this causes less damage to the stock
An ADR warehouse is a ‘product’ on its own, like a cold storage warehouse, or like an HACCP warehouse (the certification used within the food business).
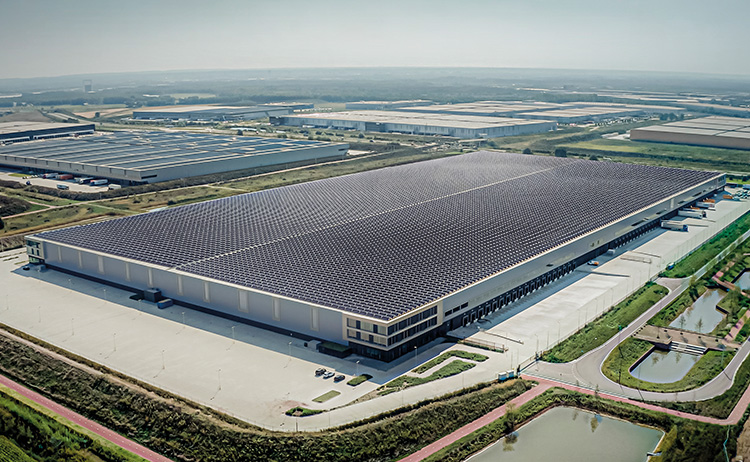
Purpose-designed dangerous goods warehousing on a large scale.
Eureka: You mentioned hazard classes. What are they?
Rene: In the Netherlands we have the so-called PGS15 Directive, which sums up the various classes. Here, the user is responsible for getting the right permits. In almost every case, the user is accompanied by an expert adviser who knows the tricky business of procedures and legislation.
The above-mentioned ADR sets out nine classes, varying from explosive substances and articles to gases and flammable liquids.
Another important European directive to follow is the Seveso Directive.

Eureka: Which are the main business sectors that have to deal with these types of goods?
Rene: The most prominent sector is probably the chemical industry, including chemical derivations like paints or lubricants. Other examples are retail chains, pharma and the food business, where citric acids are used everywhere.
Eureka: Does Next Level Development work with experts when developing these special warehouses?
Rene: Yes, we do have in-house specialists, but we also work with specialised consultants as legislation can always change. Safety officers from the client are involved as well. It’s interesting to note that we also work with the clients’ administrative personnel. The reason for this is that companies storing dangerous goods must know at any moment exactly how much is in stock. Their IT systems have to be able to provide that information promptly.
More and more products are being marked as ‘hazardous goods’ and therefore an increasing number of businesses will
have to deal with this matter.
Eureka: Earlier you mentioned that the two more simple warehouse adaptation categories require only relatively minor adjustments. Can customers organise these themselves?
Rene: In principle they can, provided they have the knowledge and experience. In practice, we often support companies to make the adjustments. This is a case-by-case service. Certainly we see an increased number of companies needing to adapt their warehouses.
Eureka: Could you sum up the standards and legislation companies must adhere to?
Rene: As in the example of the PGS15 directive in the Netherlands, every country will have its own legislation. From a European perspective, ADR and the Seveso Directive are again key.
As history has demonstrated many times, an adverse event has to happen before legislation improves drastically. A catastrophic accident in the Italian town of Seveso in 1976 prompted the adoption of legislation on the prevention and control of such accidents. The so-called Seveso Directive was later amended in view of the lessons learned from other accidents such as Bhopal, Toulouse and Enschede (fireworks!), resulting into Seveso II.
The directive applies to more than 12,000 industrial establishments in the European Union where dangerous substances are used or stored in large quantities. These are mainly in the chemical and petrochemical industry, as well as in the fuel wholesale and storage (LPG/LNG) sectors.
Considering the rate of industrialisation in the EU, the Seveso Directive has contributed to achieving a low frequency of major accidents. It is widely considered as a benchmark for industrial accident policy and has been a role model for legislation in many countries worldwide.
An interesting fact is that the directive not only aims at preventing major accidents involving dangerous substances but also provides directions for limiting consequences in the case of an accident – both for human health and for the environment.
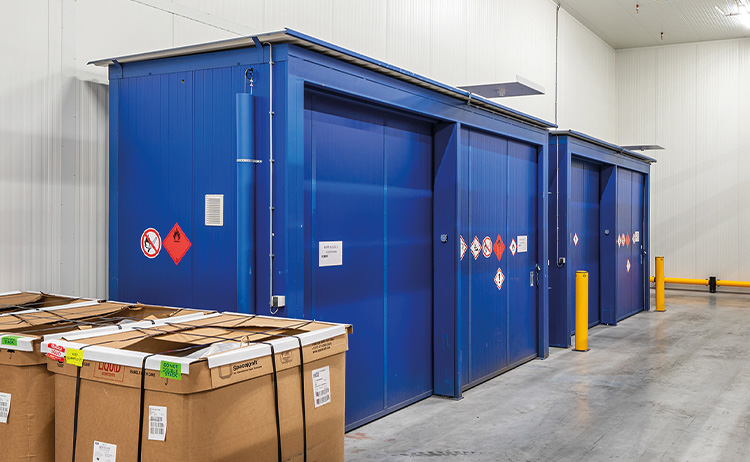
Dangerous goods containers.
Eureka: What trends do you see for this this type of logistics real estate?
Rene: In fact, more and more products are being marked as ‘hazardous goods’ and therefore an increasing number of businesses will have to deal with this matter. It starts with separating part of the stock, but dealing with these goods may well grow into a separate task within your staff.
Storing and transporting hazardous goods is no easy task. Whether adapting an existing warehouse or developing a state-of-the-art ADR warehouse from the start, it remains an evolving subject – and ever-developing legislation is reason enough to hire your own safety officer.
ADR requirements
The European Agreement concerning the International Carriage of Dangerous Goods by Road (ADR) requires:
- Extra documentation – including information on the goods, written emergency instructions and photo ID of the vehicle crew
- ADR-compliant and annually tested vehicles and tanks
- Special driver training
In addition, companies handling or transporting hazardous items may need to appoint a dangerous goods safety adviser.
Source : https://eurekapub.eu/health-safety/2020/09/24/better-safe-than-sorry
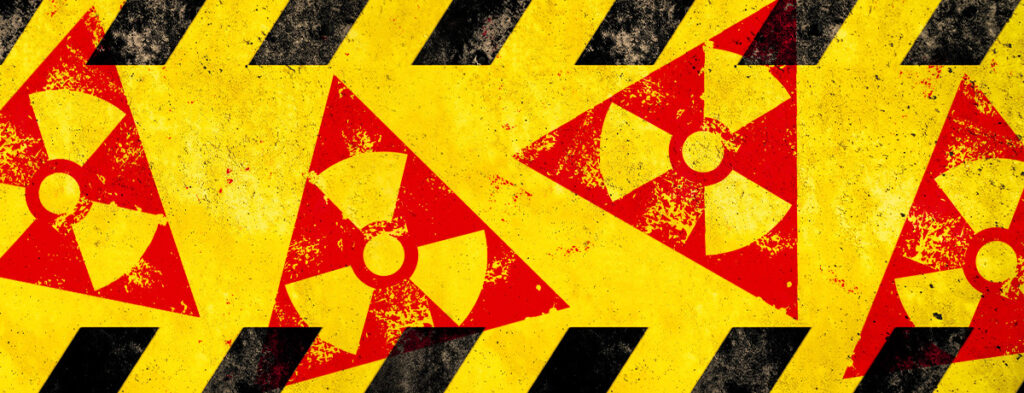