The right pick
12/03/2021
A few years ago, it seemed that each year saw the announcement of ground-breaking, revolutionary or game-changing warehouse systems. Have warehouses really changed or are the tried-and-tested methods still the best?
Order-picking remains one of the most time-consuming and costly tasks in the warehouse. It is relatively easy to shift bulk loads across hundreds of miles – all you need is a large truck, a map and some decent roads.
But the warehouse is where the loads are broken down into individual lots and it is from there that the final order will be selected, mixed, packed and delivered on time and in full – or not, if the systems aren’t up to it.
Various solutions have been put forward to make storage, picking and packing easier, more reliable and more effective. The greatest leap forward was probably the introduction of barcodes, which provided a reliable and traceable methodology, linked to electronic management systems. So – if barcodes were good, wouldn’t RFID be better? In some cases, yes, but their bulk got in the way initially. Metal in close proximity interfered with the signal, so they can be described as helpful in the right circumstances – but not a ‘magic bullet’. Their acceptance and use is spreading as they become smaller, more robust and less sensitive to a neighbouring can of beans. An alternative, the ‘bokode’ was described in eureka issue 11 and has attracted interest, not least because of its information storage capacity but it is early days, as yet, and there has been no indication of a tidal wave of acceptance. The barcode continues to be the reliable technology for warehouse management systems.
Standard pallet racking
Height and automatic vehicles
The overwhelming pressure to get the largest return for investment means making the best possible use of available space, leading to narrow aisles and high racking – which present their own challenges, including accessibility. Personnel working in high-level storage situations need a head for heights and a stable vehicle – the higher the reach, the more that sway will come into play.
Double-deep racking
The barcode continues to be the reliable technology for warehouse management systems
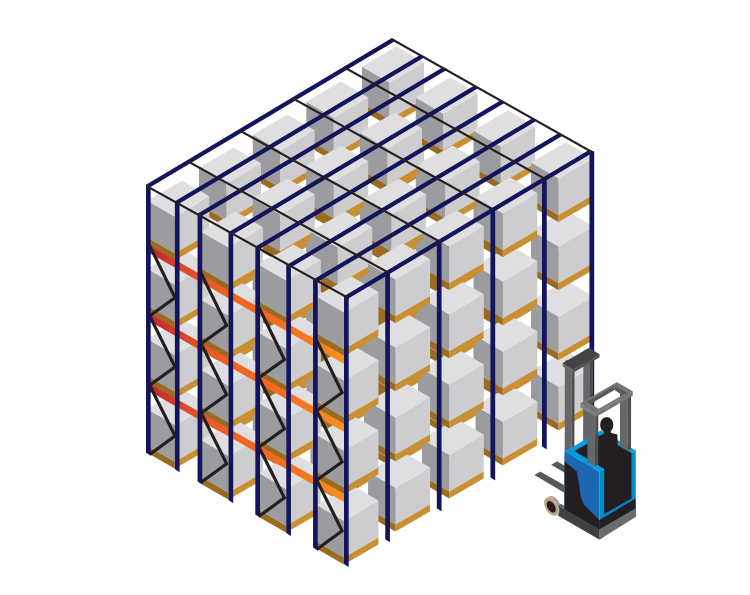
Drive-in racking
Racked for choice
In terms of physical layout of racking, the permutations are, in essence, made up of variations on six types. Standard adjustable pallet racking is the simplest, allowing set positions for individual pallets. Double-deep racking increases the density of storage but only half the total number of pallets are accessible at any time. It works well in kanban systems and where larger amounts of product lines are held in store and goods move reasonably quickly. Pallets are stored on longitudinal beams in drive-in racking systems, which dispense with conventional aisles but restrict access to only the nearest units. ‘Live’ or gravity-storage systems store pallets several-deep on inclined rollers, which are loaded from the back. Rearward units automatically slide forward as the front pallets are removed. It is a relatively simple solution that ensures first-in-first-out (FIFO) stock rotation. Pushback racking also uses gravity but as it is fed and unloaded from the front, it is not appropriate for situations where stock rotation is critical. Finally, mobile racking uses powered rails; racks are moved to allow access to the desired shelves. It allows maximum density but access is restricted.Assessing risks
Controlling risks
Understanding responsibilities
Understanding hazards
Investigating incidents
Measuring performance
Protecting our environment
How should manager training be delivered?
Unless a course is presented in an interesting and practical way, and made relevant to the participants, it won’t achieve much. The IOSH course, for example, includes videos, games and exercises to engage people’s minds and reinforce messages. Managers are also given a work-based project, to assess an aspect of their operation and reduce its risks. Importantly, those taking a course should be assessed and, if they pass, given certification.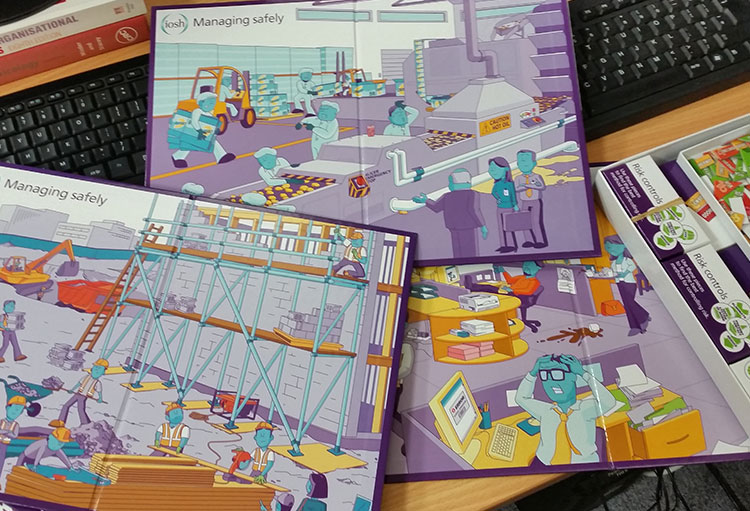
To be effective, courses need to be relevant and interesting. Exercises and games can help to engage thought.
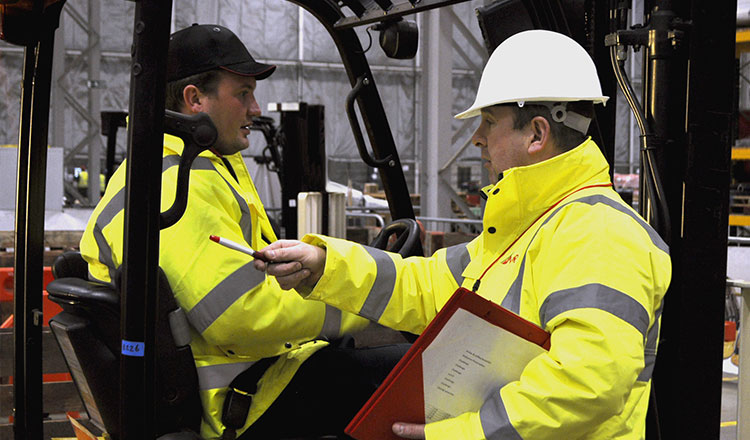
A manager supervising a forklift operation should appreciate the risks and know what is good and bad practice. Photo by courtesy of Mentor
Where can you go for help?
Mentor mainly trains professionals in the UK, but others can still obtain information and advice via its website www.mentortraining.co.uk. RCES provides international consultancy services and can be contacted via www.rces-ltd.com. IOSH – website www.iosh.co.uk – has members worldwide and will be happy to advise. A good starting point for guidance in any EU country is the European Agency for Safety and Health at Work (EU-OSHA). Its website www.osha.europa.eu gives details of a ‘focal point’ in each country – typically the competent national authority for safety and health at work. Source : https://eurekapub.eu/health-safety/2018/02/06/are-you-managing-safelyIn terms of physical layout of racking, the permutations are, in essence, made up of variations on six types.
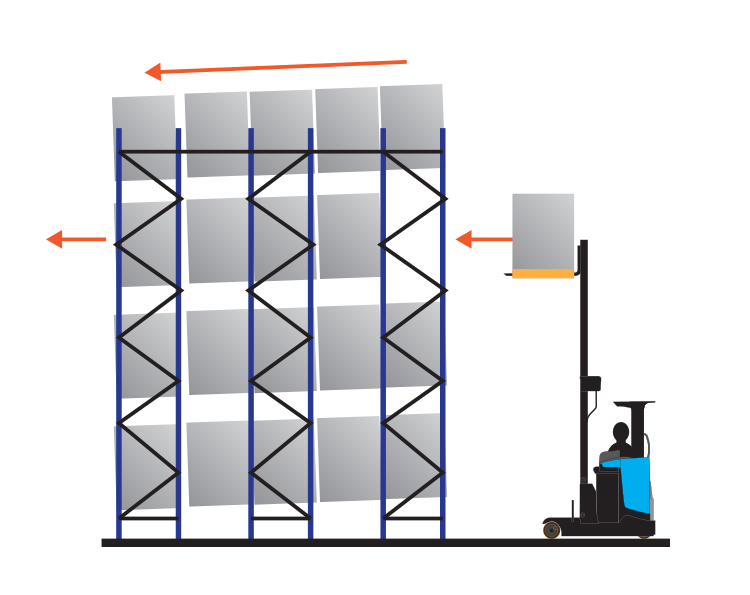
Live/Gravity-storage
Safer protection
“Another area of interest is racking protection and protective barriers made out of super strength polycarbonate,” said Paul Fox. “This is an area identified by customers as a massive expense in terms of damage to racking and fork trucks themselves. We are speaking to the world-leading manufacturer of this type of product, in order to assist our customer base with safety and reduced damage costs. The polycarbonate product is stronger than steel and doesn’t bend; trucks effectively ‘bounce off’ them, but safely.” With all these choices available, which is the right solution?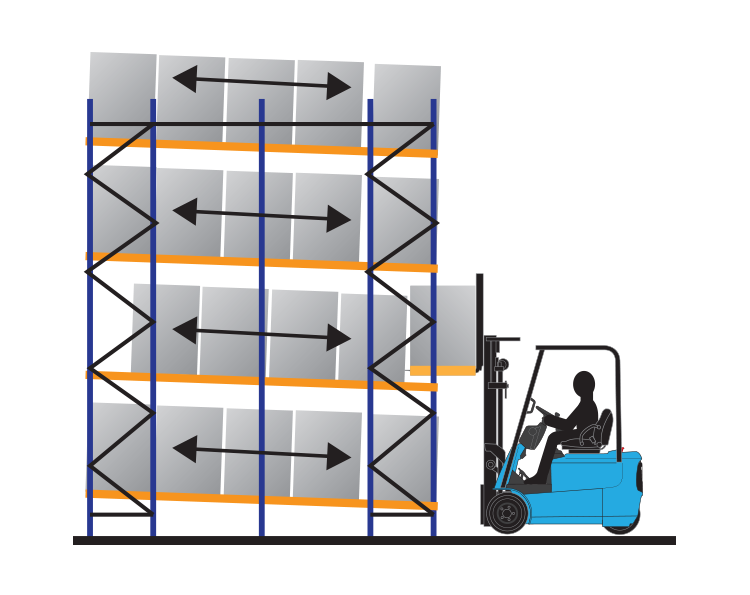
Pushback racking
“Another area of interest is racking protection and protective barriers made out of super strength polycarbonate”
Getting it right, first time
“A fully automated warehouse will work extremely well when all products have common dimensions and weights and the products are going to be produced in the longer term,“ said Martijn Ligtvoet, warehouse consultant with Dutch Cat lift trucks dealer, Crepa BV. An integrated, fully-automated warehouse is fast, very reliable and delivers big savings in flow handling time – but no two circumstances are exactly the same. Crepa in the Netherlands, Aprolis in France, Bergé Manutención in Spain and Compagnia Generale Macchine S.p.A in Italy all undertake site surveys to help customers achieve the optimum solution. It will balance manual and automatic operations with storage density in order to achieve the best use of space, personnel and the right mix of trucks for most effective operation.
“A fully automated warehouse will work extremely well when all products have common dimensions and weights”
Mobile racking
The site survey examines the total costs of process and how the logistics flow. Some dealers also use simulation software, which is a useful tool for showing the customer a visual presentation of how efficiency can be improved, together with financial calculations of the total operation.
Source : https://eurekapub.eu/technology/2011/10/11/the-right-pick
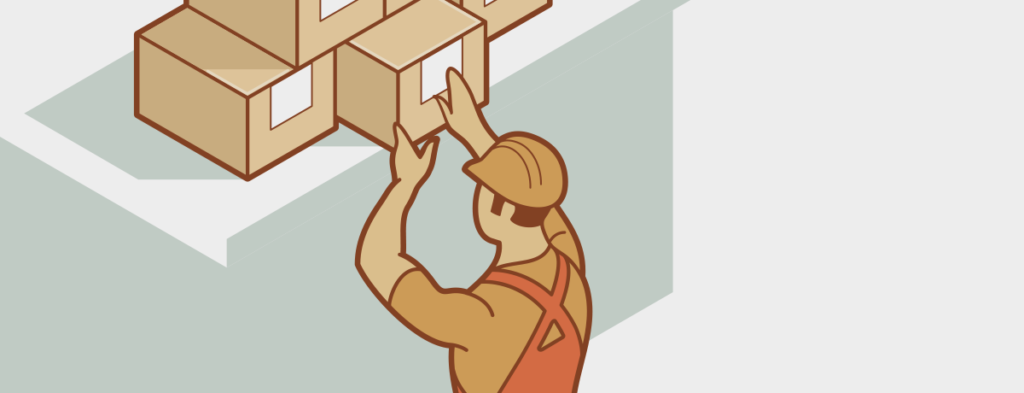